One Stop Solution
We integrate co-product design services, mold development, prototyping, testing, homologation, production, and assembly, offering a complete solution from concept to mass production. Through an integrated approach, we ensure that each stage of the development and manufacturing process is perfectly coordinated, optimizing both for quality and efficiency.
-
Production and Assembly
Manufacturing of the various parts and assembling them into the final component.
-
Co-product Design
Collaboration for product design development.
-
Homologation
Certifying component compliance with initial standards.
-
Mold Development
Creating the necessary molds for production.
-
Testing
Verifying component quality and performance.
-
Prototyping
Creating prototypes for testing and evaluation.
From Concept to Mass Production.
All in One Industrial Platform.
Zero Carbon Footprint.
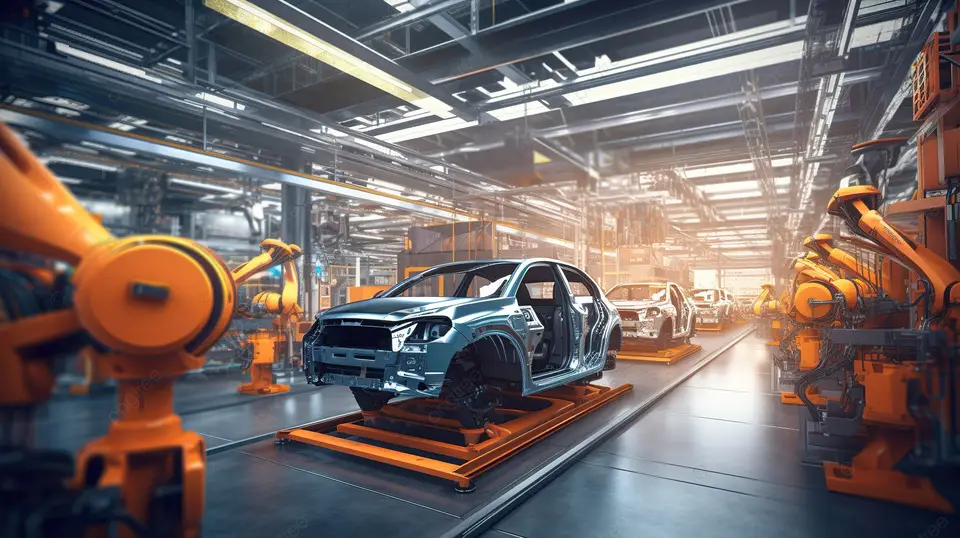
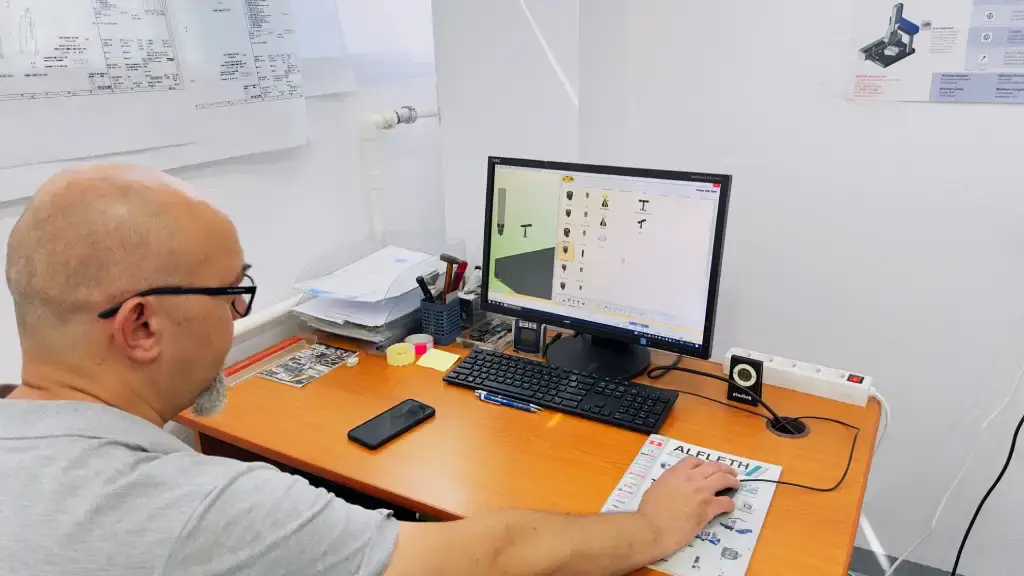
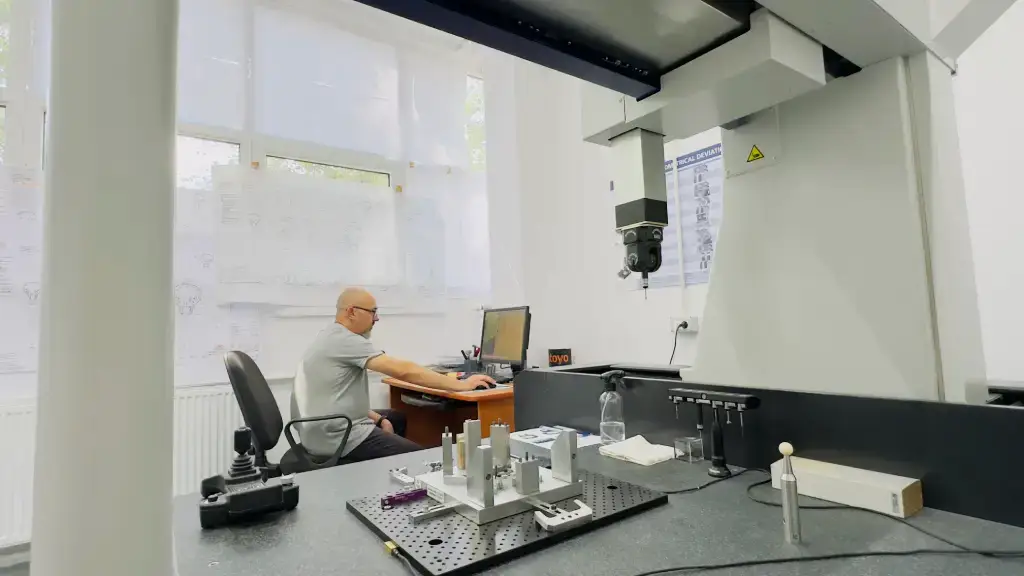
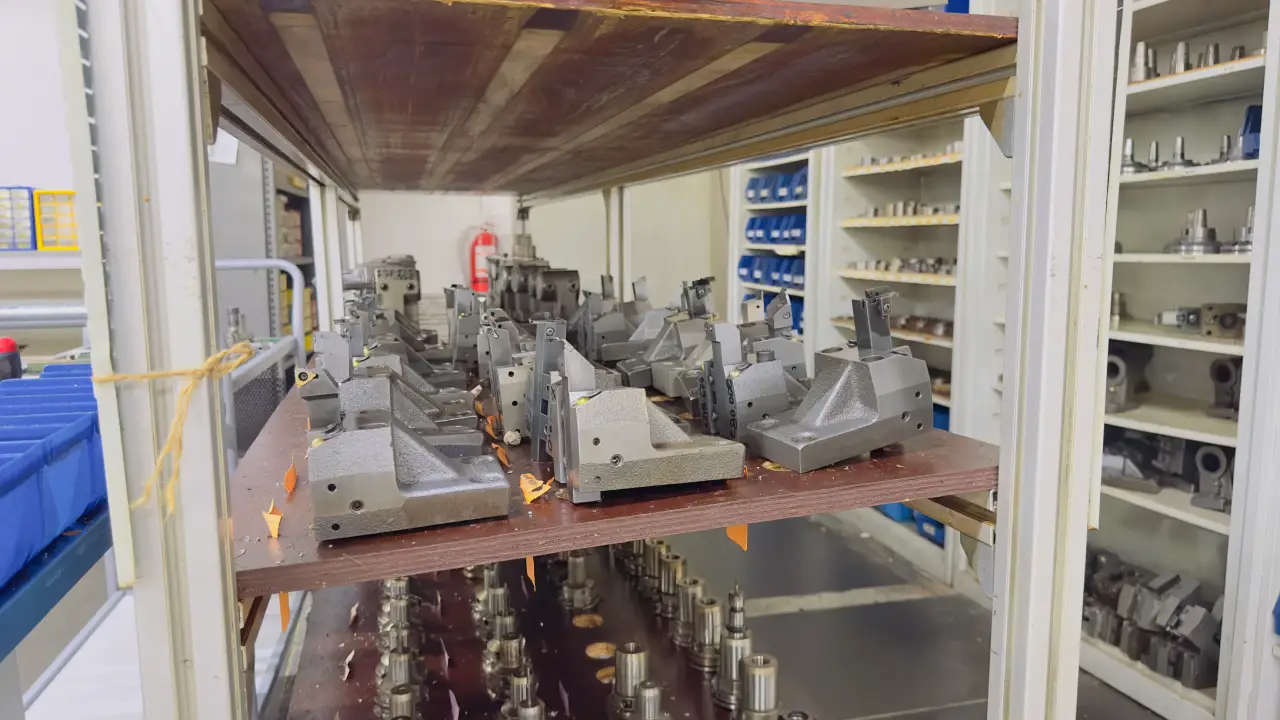
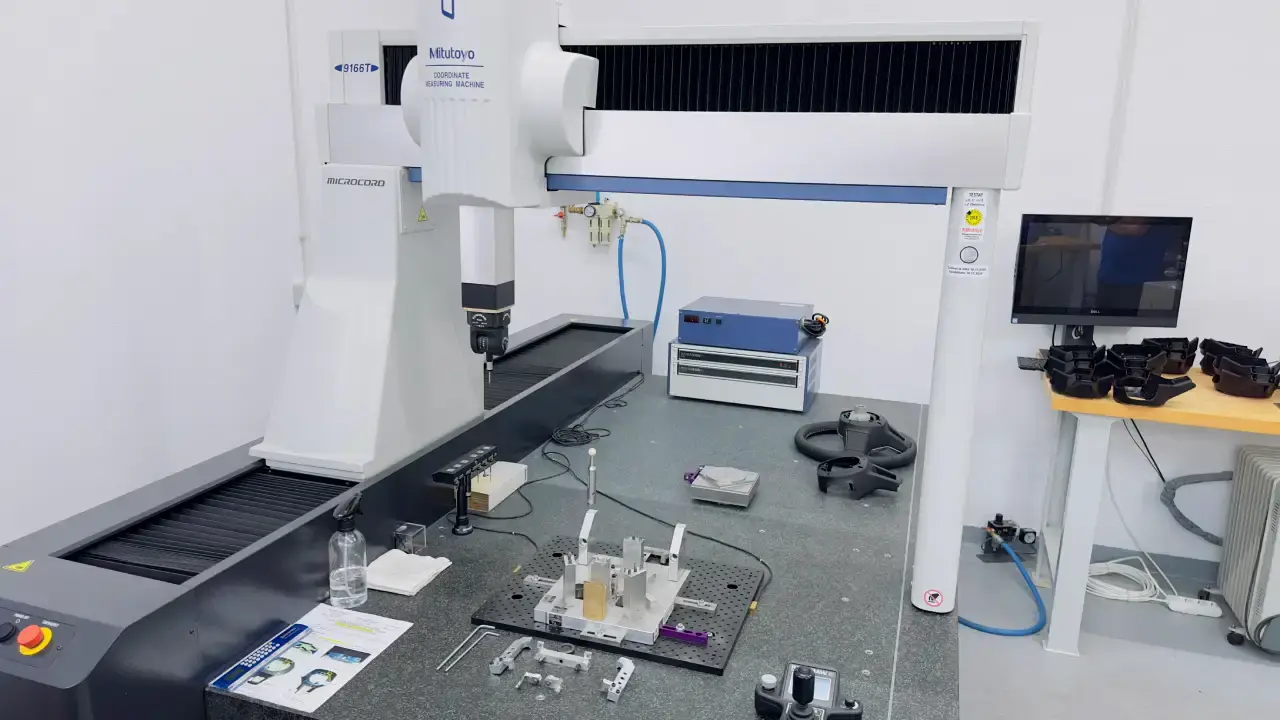

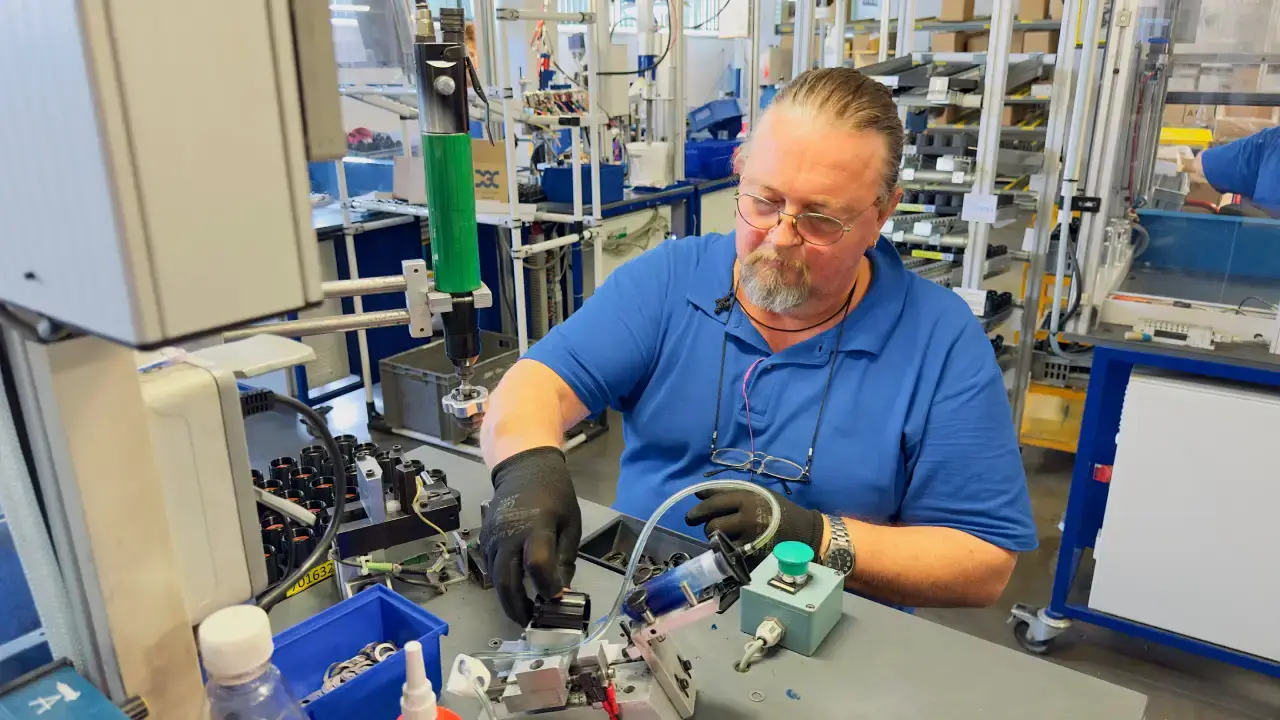